Historically, many freezer alarm probes have been inserted into small glycol buffering bottles. Why? The glycol solution serves as a buffering agent to deliver accurate readings that better reflect the actual temperature of items stored inside the freezer.
Let’s dive a little deeper into the advantages of using glycol for temperature probes.
Why Use Glycol Bottle as a Buffering Agent for Temperature Probes?
Helpful Delays
When the door of a freezer is opened and much warmer room air reaches the sensor bottle, the thermal mass of the bottle and glycol takes time to warm up. This delays the sensor reading going into the alarm range and subsequent alerts being sent. Without the glycol as a buffering agent, the sensor’s temperature would rapidly climb, setting off the alarm in short order.
Most freezers now embed the internal temperature sensor into the bottom of the freezer cavity, so the thermal mass of the cabinet interior acts as a large buffer, delaying the alarm. These same freezers also usually have a variable alarm delay capability that can be set through the front display to provide an even longer delay before the audible alarm goes off.
Temperature Accuracy
The typical samples stored in a freezer are quite small, having a small thermal mass, so they too take awhile for warm room temperature air to raise their temperature. Having a small buffering agent like glycol with a similar thermal mass to the samples allows the alarm to trigger when the agent reaches alarm levels that should match the sample temperature.
Regulatory Measures
Several state regulatory agencies still require buffering agents to be used for vaccines and some other medications. These measures ensure alarms go off appropriately when the vaccine temperature reaches a critical threshold. As a buffering agent, glycol acts as an analogue to the vaccine serum.
Buffered Readings Vs. Measuring Freezer Cavity Air Temperature
Measuring air temperature in a freezer cavity is a much more sensitive method. As a freezer door is opened and warm room air comes into contact with the temperature probe, the probe immediately senses and reports the rising temperature.
To prevent alarms from going off every time the door is opened, a time delay threshold must be exceeded while the temperature remains above alarm levels. Since the air temperature inside the freezer cavity very quickly returns to normal levels once the freezer door is closed, selecting the proper alarm time threshold will prevent alarms from going off every time the door is opened. This time threshold should be longer than the typical time a door is open while adding or removing samples (typically 20 minutes).
The Benefits of Measuring Air Temperature
One advantage of measuring air temperature is that it allows insight into the health of the freezer. When the door is closed and the freezer is operating normally, the temperature inside the freezer slowly rises until it hits the set point for the freezer, and the compressor turns on to cool off the freezer. Once the temperature is low enough, the compressor turns off and the freezer very slowly starts to get warm again. Depending on the freezer and the thermal mass of its contents, this on/off cycle can be anywhere from 10 to 40 minutes.
When the freezer is working properly, this temperature regulation produces a consistent temperature “sawtooth” pattern, showing a slow, smooth temperature increase, and then typically a slightly more rapid temperature decrease when the compressor is on and cooling the freezer. Seeing graphs of this sawtooth pattern makes it easy to spot anomalies and even see if the cooling off cycle is now taking longer than before, which can be indicative of leaky door gaskets or a compressor problem that will probably get worse.
Another advantage of this method is you can watch the rate at which the temperature decreases once the door is closed after being opened. Over time, a pattern emerges and deviation from the normal temperature recovery pattern can also indicate gasket or compressor issues.
It’s worth noting that changes to the thermal mass of the contents inside the freezer will change the slopes of the sawtooth pattern. The more thermal mass in the freezer, the longer the on/off cycle and the sawtooth slopes will not be as steep. Comparatively, with less thermal mass in the freezer, the on/off cycle is shorter and the sawtooth pattern is steeper.
Here is a graph of a new -80℃ freezer with few samples inside, and a small thermal mass.
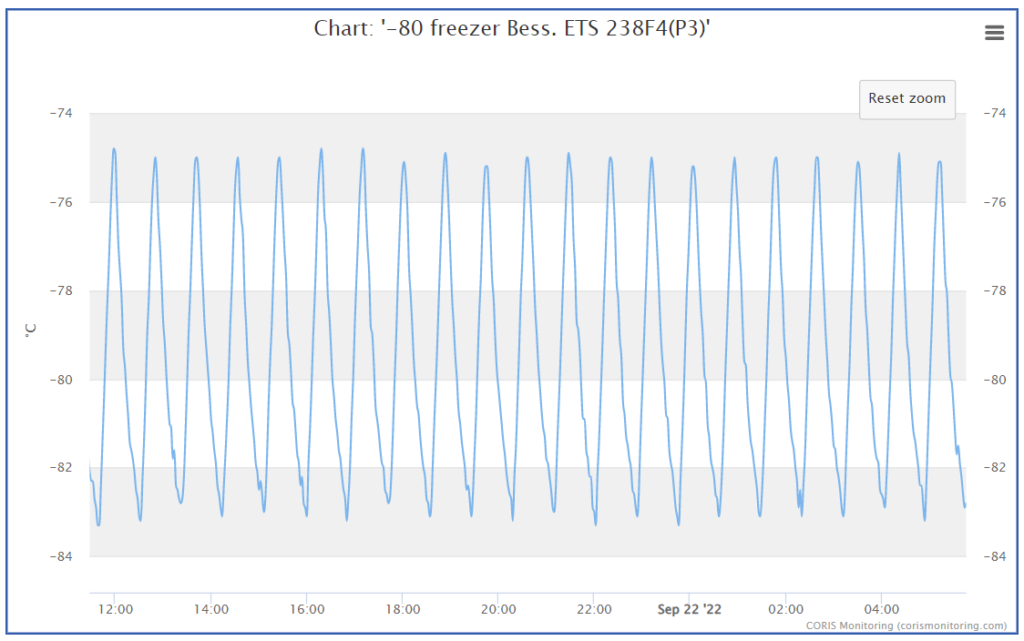
Have temperature monitoring questions? Connect with CORIS and see how our state-of-the-art system can support your monitoring needs.